Monitor and detect CUI
CUI Spotter
Monitor and detect corrosion under insulation with CUI Spotter and you can warn the plant manager far before leakages occur. Install one single sensing cable under the thermal insulation and monitor at least three hundred meters of line.
There is no need to permanently install measuring instruments, no need to replace batteries or connect to wireless networks. In short, you can carry out measurements every few years using a TDR portable instrument.
In addition to pipelines, you can install CUI Spotter around heat exchanger shells, above-ground tanks or columns.
Why should I monitor and detect corrosion under insulation-CUI? Can you not rely on inspections?
Normal inspections are not effective in detecting CUI. For instance, studies show that inspections can find five CUI locations for every thousand critical points inspected. Choose to monitor corrosion under insulation with CUI Spotter 24/7 and increase the reliability and safety of your installation.
CUI is extremely costly for industrial installations both in terms of maintenance and operation interruptions. In other words, a mid-size refinery in Europe would spend more than one million euros per year on CUI maintenance.
Thanks to its patent-pending design, CUI Spotter is currently the longest, most reliable and simplest corrosion under insulation sensor. In conclusion, CUI Spotter outperforms its competitors in many aspects.
CUI Monitoring Systems and CUI Spotter
When we started thinking about developing a sensor to monitor corrosion under insulation, we also considered possible alternatives.
In fact, each technical solution has its advantages and disadvantages.
Since at CUI Spotter we believe in ideas, knowledge and clearity, we will show you the logical path that led us to the creation of a sensor of this type.
After years of experience in the industry we had heard of various technologies that hadn’t been successful.
Previous unsuccessful innovations not able to monitor and detect CUI
About 20 years ago, a well-known European research center, developed CUI visual sensors. These sensors were installed every 10-20 meters at 6 o’clock of the cladding, and their color would change when humidity was present in the insulation.
Corrosion is more than just humidity.
The limits were clear. After the application, the installers realized the unreliability of the idea. In fact, after years of use, these sensors were intrinsically prone to moisture absorption and sooner or later they would change colour. Corrosion under thermal insulation is not a failure mechanism with a high likelihood of failure, but with a high consequence of failure (read API 581 to learn more about the topic). This means that it can take many years for an event to occur on of line. To conclude, these sensors had a short life and the unavoidable absorption of humidity over the years led to their unusability. It was clear this sensors were not able to monitor and detect CUI in a reliable way.
Optical fiber sensors? Are they able to monitor and detect CUI?
We knew, as did many people in the industry, that you can use optical fibers for leakages monitoring. In addition, optical fibers also allow for temperature monitoring. Some sensors even allow the monitoring of temperature and humidity at the same time. Were optical fibers also able to indirectly monitor and detect CUI?
During the time I was developing my sensor, I spoke to an old friend of mine who was a student like me during my PhD at Cranfield University (I am sure you want to read my PhD thesis…here is the link…). My friend has had a better career than me and he is currently a professor of Optical Fibre Sensing at a major British university. With him, we discussed the possibility of using optical fibers and the conclusion was that the technology was valid but not robust enough for use in an industrial plant.
It is a factory, not an internet fiber network
Optical fiber are expensive and are sensitive to bending. After installation, you would at least need one zero measurements to avoid difficulties in interpreting future data. This would involve storing data, maintaining a database for the different sections of sensors used, etc. Furthermore, the need to measure the fiber optic cable continuously was indispensable. This meant installing expensive battery-operated wireless tools, with all the hassles of battery life and replacement.
Companies are less good at scheduled maintenance
My experience in the industry told me that many companies are good at initial installations, but the scheduled maintenance of sensors is not always in the foreground. Especially when it comes to long-term problems such as corrosion. In conclusion, I abandoned the idea of optical fibers. Optical fibers sounded too fancy, too expensive, and unpractical . I thanked my friend and I went back to thinking…
Capacitance measurements? Can you use them to identify and monitor CUI?
Since I had heard about some complicated techniques for detecting water at various CUI conferences, I began to think about the possibility of detecting the presence of water under the thermal insulation. I have to say that the idea didn’t excite me at first.
It is true that the presence of water is a necessary factor for CUI, but not sufficient. In fact, the temperature also plays an important role. I had read scientific publications about the possibility of considering cladding, pipe and wet thermal insulation as a capacitor. In fact, we are talking about two conductors separated by a dielectric. It was clear that by connecting the tube and the cladding to a simple capacitance meter, we could detect the presence of water.
Corrosion is more than just water.
However, the theory is often far from practice and the various cladding panels are not always electrically insulated from each other. Especially in old systems, dozens of panels are in electrical contact. Therefore, you would not be able to define the capacitor characteristics that you need to calculate its capacitance and the presence of water. Furthermore, you should monitor changes in the capacitance continuously with the installation of a wireless capacitance meters.
Again the battery problem and the intrinsic unreliability of the measurements. Not what you need.
Monitoring changes in the impedance of a conductor. Sophisticated but with too many limitations. Not a reliable solution when you want to monitor and detect CUI
When I started thinking about the CUI Spotter, I studied the TDR for quite a long time. I found an article from the Bari Polytechnic, where studies had been made to identify the impedance variations for a metal conductor installed under the thermal insulation. With this system, you could locate the presence of water.
Despite this, the length of the sensor was only a few meters. Furthermore, the measurement results were difficult to interpret and required the use of Frequency Domain Reflectometry (FDR), a more sophisticated version of Time Domain Reflectometry (TDR) used for CUI Spotter. Additionally, and again, the sensor required continuous monitoring with the consequent installation of dozens of wireless, waterproof, battery-powered FDRs.
Expensive, complicated and unreliable. Especially since the user should trust the software that analyzes the data and modify his CUI inspection campaign on the basis of these data. It didn’t seem like a solution that would be easily accepted by our “conservative” maintenance engineers.
Simple, strong and reliable. Learn how we monitor and detect CUI in the simplest possible way
It was clear that all the solutions considered needed the installation of measuring instruments every few tens of meters and constant maintenance of the aforementioned.
Practice collided with theory. I wanted a simple, reliable solution that didn’t necessarily require the installation of measuring instruments on the line and above all I wanted easy-to-read data, even for an operator.
A corrosion sensor designed by a corrosion engineer. The way it should be.
As a corrosion engineer, I have never liked being dependent on consultants, contractors and external experts. Maybe I’m old-fashioned. So I thought about installing a simple metal wire in the thermal insulation. If the conditions existed to cause corrosion on the pipe, the conditions would also exist to cause corrosion on the wire. How to locate the position of the interrupted wire? And how make the wire, despite being steel like the tube, corrode faster than the tube? The solution was the creation of a coaxial cable permeable to water, where only the internal part corrodes thanks to the galvanic coupling with the external part. This coaxial cable would be able to monitor and detect corrosion under insulation in a simple and reliable way.
Using galvanic corrosion to monitor and identify corrosion? Right!
Surely my PhD on galvanic and electrochemical corrosion helped me in the logical process. Furthermore, not only did coaxial cable allow two different materials to be incorporated to generate galvanic corrosion, but it also allowed it to be monitored using a TDR instrument. Unlike the other options though, the tool didn’t have to be installed permanently. In fact, there was no need to monitor the evolution of the signal.
In the presence of CUI, the coaxial sensor would break in a few months, and periodic measurements with intervals of even a few years would allow the location the exact point to be repaired. That is the point where CUI was present. You could then repair the locally with a connector and use it again.
Simple, reliable and cheap. TDR tools are a little more difficult to use than a simple multimeter. With a bit a training my eight years old son could do it…it would take a bit longer for the younger one…
Is CUI Spotter the perfect CUI monitoring system? Can I use it anywhere?
Like all things, nothing is perfect. CUI Spotter is the ideal sensor for new installations. It is cheap, reliable, and it requires no maintenance until it breaks. And yes, when it breaks it’s when you’ve found CUI!
What about existing installations? Can I install CUI Spotter?
As mentioned, CUI Spotter is the ideal solution for new installations. Nevertheless, the sensor can be retrofitted. By applying a longitudinal cut at six o’clock of the cladding, it is possible to insert the sensor in the insulation. The cladding can then be repaired with a metal sheet installed with automatic riveting. The procedure is fast and simple. In any case it must be performed during a Turn-Around, as cladding cutting can only be performed in areas with low ATEX classification.
The 70's oil crisis
In the 70’s the oil crisis and the increased cost of energy forced the industry to reduce energy consumption and become more efficient.
In conclusion, piping and equipment insulation became common practice to reduce heat losses.
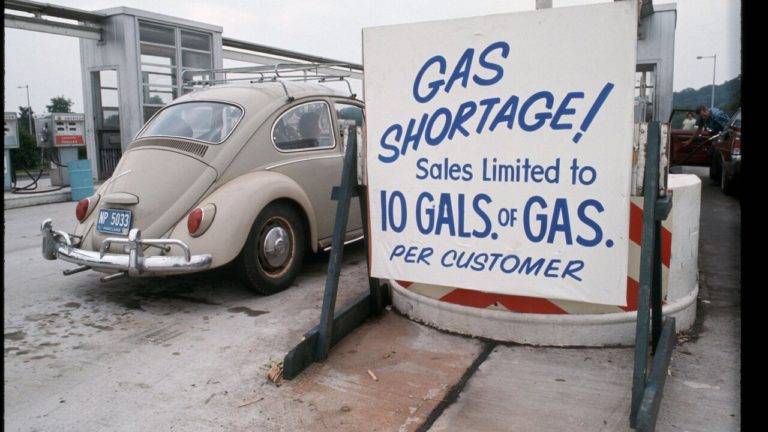
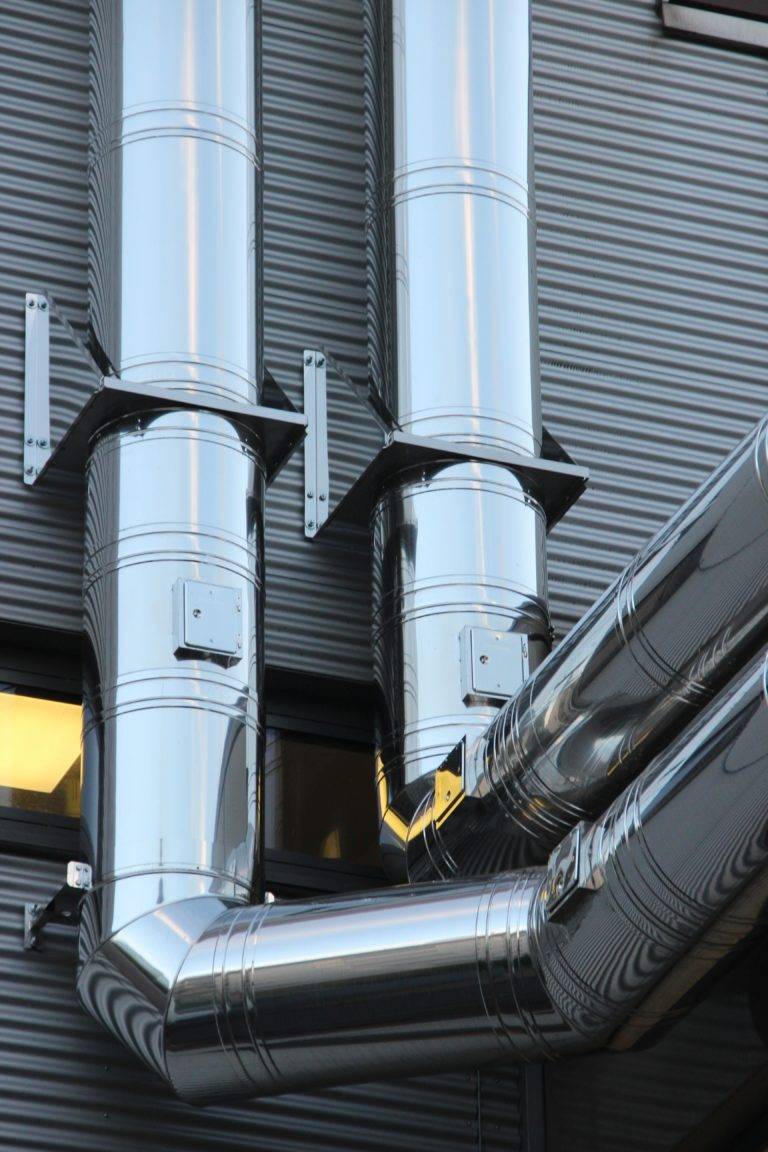
New insulation will get older. You will have to monitor and detect CUI
Thermal insulation is mostly made of hydrophobic mineral wool. Nevertheless, after many years in operation, the mineral wool tends to lose its hydrophobicity.
A metal sheet cladding usually covers the mineral wool to protect it from rainwater. The cladding installation and design are often not idea allowing water entering the insulation.
Monitor and detect CUI before a leakage occurs
Often water enters the insulation meters far away from where it accumulates and no damage is visible without removing the insulation.
Especially at temperatures close to 100 degrees Celsius, protective coatings will only give protection for a few weeks. In short, after the coating fails, carbon steel will corrode relatively quickly, leading to leakages.
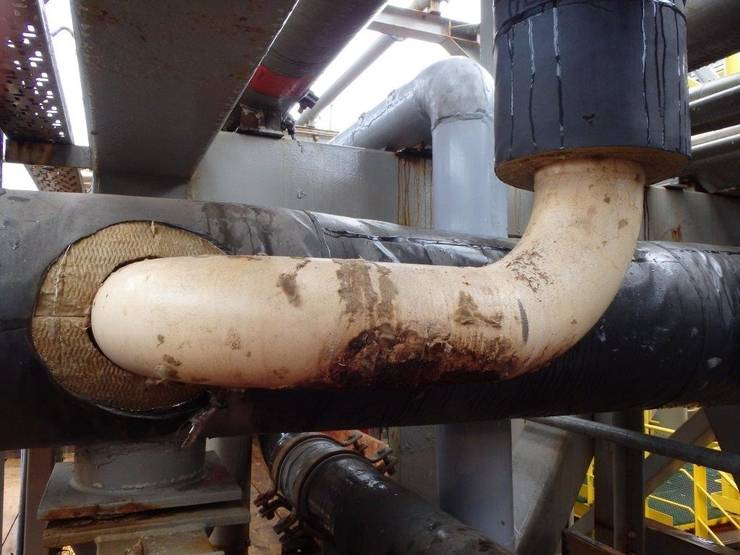
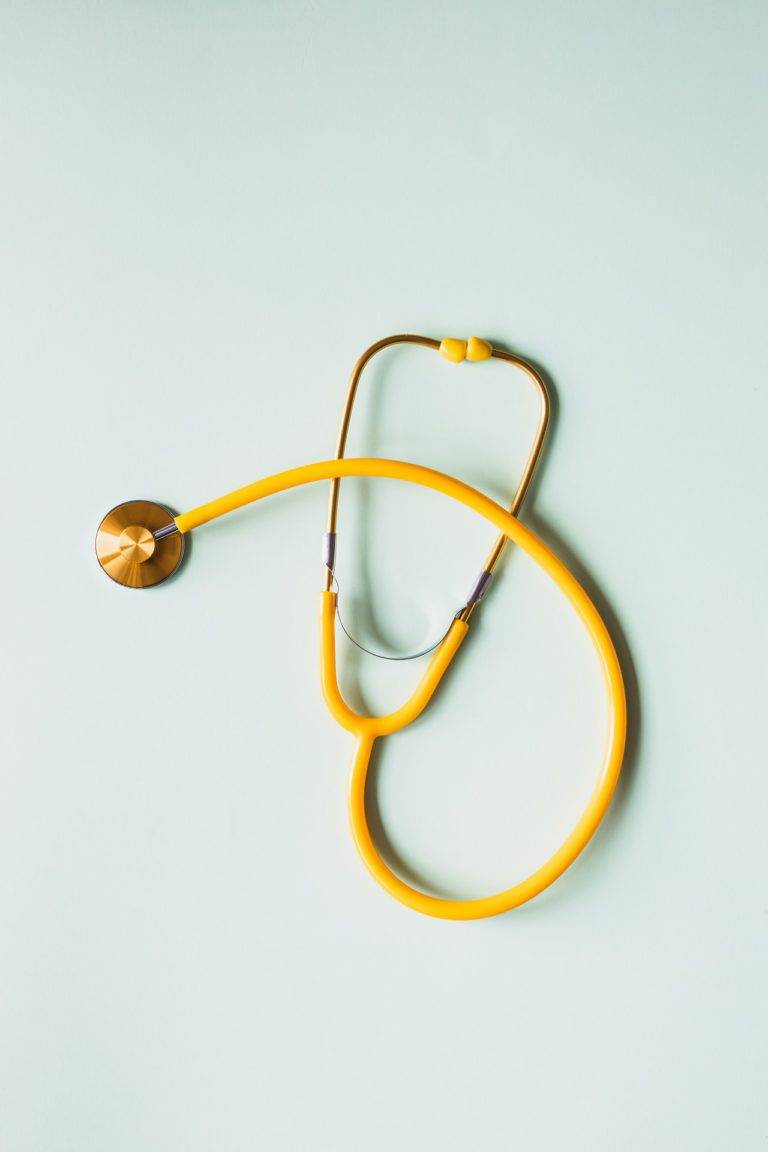
Alternative approaches are not able to monitor and detect CUI. At least not efficiently.
There are currently no effective and reliable methods to detect corrosion under insulation. Companies usually rely on inspections, periodically removing part of the insulation on what are considered critical points, such as elbows or lower points.
Unfortunately, studies show that only 0.5% of the inspected critical points show CUI.